【22-39】フロー・システム最適化で工業生産の省エネ・排ガス削減を実現へ
李 禾(科技日報記者) 2022年09月07日
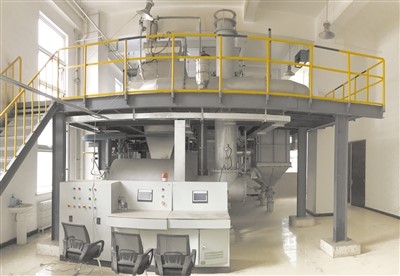
ダストを含む高温ガス・排熱回収一体化試験プラットフォーム
画像提供:取材先
中国では工業のエネルギー消費量が社会全体のエネルギー消費総量の約65%を占めており、工業システムの省エネを実現すれば、化石燃料使用の減少につながり、発生源から二酸化炭素の排出を減らすことができる。
排ガス・排熱の回収と浄化をめぐる難題をまとめて解決
製鉄やセメントの焼成、リアクターを用いた化学工業製品生産などは大量のダストを含むガスを排出する。そのガスの温度は800℃--1200℃に達し、排熱は高品位のものだ。
重慶大学エネルギー・動力工程学院の廖強院長は、「冶金、建材、エネルギー、化学工業といった業界のエネルギー消費量は、中国の工業のエネルギー総消費量の70%以上を占めている。うち、排ガスと未利用エネルギーが工業消費量の17%を占め、年間平均3億4000万トンの標準石炭を消費しているのに相当する。工業のダストを含む高温ガスの排熱回収効率を向上させる技術は、中国内外でも技術的難題となっている」と話す。
このほか、上述した業界の排ガスに含まれているダストの量は年間634万3000トンに達し、工業のばい煙排出量の50%を占めている。
そのため、中国国家重点研究開発計画プロジェクト「工業のダストを含む排ガス・排熱回収技術」のサポートの下、重慶大学や北京科技大学、中国科学院過程工程研究所といった科学研究院(所)10機関の専門家と企業の研究開発者からなるプロジェクトグループが共同で難関攻略に取り組んでいる。
廖院長は、「排ガスの性質に基づいて、凝縮性ダストを含む排ガス、大量のダストを含む高温排ガス、低濃度のサブミクロンサイズのダストを含む排ガスの3種類に分類した。研究チームは、3種類の排ガスのそれぞれの特徴に合わせて、高温ダスト凝縮自己制御粘着収集・動的定向脱着交換技術を編み出し、ダスト凝縮低油圧抵抗連続化濾過と排熱の一体化回収を初めて実現した。また、階段型の隙間構造がある3D超特大表面拡張ハニカム構造新型蓄熱、熱交換体パーツ、超特大表面拡張機能のある防摩耗・ダスト除去3Dリブパイプ強化伝熱技術を編み出し、3D超特大表面拡張蓄熱、熱交換機能を持つ大量のダストを含む排ガス連続高効率排熱回収・浄化一体化技術を確立した。このほか、高温低濃度サブミクロンサイズ粒子を高度に浄化できる新型コーティング材料調製技術を開発し、コーティング材料の温度使用制限をめぐるボトルネックを打破した」と説明する。
そして、「こうしたキーテクノロジーを今後5年活用すれば、世界の工業の高温で大量のダストを含む排ガス・排熱回収・浄化技術の発展をリードできるだろう」との見方を示す。
プロジェクトグループは、理論と技術、設備、応用モデルが一体となった独自の知的財産権を持つ技術体制を構築した。それをベースにして、高温で大量のダストを含む排ガスの高度浄化と高効率の一体化テクノロジーインテグレーション、ユニットエンジニアリングモデルを初めて実現した。モデルプロジェクトの運営を通して、凝縮性ダストとサブミクロンサイズのダストの量が1立方メートル当たり7万4000マイクログラムの高温排ガスの連続高効率回収・浄化を実現した。排熱回収率は平均82.27%で、浄化後、排ガスに含まれるダストの平均濃度は1立方メートル当たり4.82マイクログラムとなっている。工業のダストを含む排ガス・排熱回収技術は現時点で、発電や冶金、セメント製造といった分野の企業20社以上で応用されている。ここ3年近くにわたり、生産高は2億3000万元(1元は約20.1円)、利益は5000万元以上、税収は3000万元近くに達し、標準石炭約45万トン、二酸化炭素の排出を約120万トン、それぞれ削減した。その応用の見通しは非常に明るい。
新技術の推進・拡大後、鉄鋼10億トン生産で約3000万トンの標準石炭削減見込み
鉄鋼業は中国の製造業の中で、石炭消費が最も多い産業で、中国全土の工業部門の一次エネルギー消費総量の約15%、二酸化炭素排出量の約16%を占めている。鉄鋼業の省エネ・排ガス削減は、二酸化炭素(CO2)排出量ピークアウトとカーボンニュートラルの目標を達成するために不可欠なものなのだ。
鉄鋼業の生産には、製鉄、製鋼、圧延といった複数の工程があり、その生産の過程は途切れることなく連続している。北京科技大学の郭占成教授は、「そのような特徴があるため、鉄鋼業の生産のフロー・システム最適化及び界面接合のキーテクノロジー、設備開発は、省エネ・排ガス削減において重要な役割を果たす」と説明する。
そのため、中国国家重点研究開発計画プロジェクト「化学工業冶金フロー工業システム最適化・省エネ技術」は、鉄鋼業の生産過程を主体に、製鉄--製鋼、製鋼--連続鋳造、連続鋳造--圧延といった工程間を合理的に組み合わせ、動的運営を最適化し、人工知能制御技術と組み合わせて、さまざまなユニット界面のエネルギーフロー、物質フローの管理コントロールを最適化したシステムを開発した。
河北省唐山市にある首鋼京唐公司は、全フローで、一体化調整・コントロール原則に基づく動的調整・コントロールを行なっている。取鍋、鋳造識別・位置測定を通して、鉄鋼の製造工程・物流のスマート化感知追跡や、取鍋の回転、鋳造の調整を通して、生産過程の物流スマート化意思決定管理・コントロールを実現している。また、エネルギー媒質の合理的な配分を通して、鉄鋼の生産過程の物質フロー、エネルギーフロー、情報フローの連結・配置を実現している。
郭院長は、「こうした技術を首鋼京唐公司で応用してから、鋼1トン当たり30キロ近くの標準石炭を削減し、省エネ効果は約5%となっている。プロジェクトでは、タンディッシュ誘導加熱技術・設備の開発に成功し、中国の鉄鋼生産の空白を埋めた。包頭鋼鉄集団といった複数の鉄鋼企業での実践、応用を経て、輸入設備よりもエネルギー効率が10%以上高くなった。また、従来的な鉄鋼生産において副生されるガスの利用効率が低いという問題に焦点を当て、プロジェクトでは、コークス炉ガスを主なエネルギーとするメタクリル酸メチル合成新工法を開発し、1千トン級の技術モデルに成功。独自の知的財産権を有する新工法を確立し、鉄鋼業と化学工業が石炭を段階的に利用するために、キーテクノロジーを提供している」と説明する。
そして、「こうした技術と設備が中国全土の鉄鋼メーカーで応用されれば、鉄鋼を年間10億トン生産するとして、約3000万トンの標準石炭を削減できる可能性を秘めている」と強調した。
※本稿は、科技日報「流程系統優化譲工業生産節能減排」(2022年8月8日付4面)を科技日報の許諾を得て日本語訳/転載したものである。