材料力学特性のレーザ制御
2012年1月5日
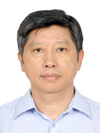
陳光南(Chen Guangnan):中国科学院力学研究所研究員
1948年11月生まれ。1991年、北京航空航天大学航空・宇宙工学製造過程を専攻、工学博士号取得。「圧延ロールのYAGレーザダル加工技術及び応用」プロジェクトの主要メンバー。本プロジェクトは1997年度「中国特許発明創造金賞」を受賞(世界知的所有権機関(WIPO)及び中国特許局により共同授与)。2007年に中華人民共和国科学技術発明賞2等賞を受賞。「内壁の管状作業レーザ強化技術」プロジェクト責任者。2008年度「国防科学技術発明賞」3等賞を受賞。
1 はじめに
強度と靱性、表層と基底、そして局部と全体の性能バランスは金属加工品の使用性能及び耐用年数を決める重要な要素であり、材料加工や機械製造等の業界で普遍的な製造技術上の難題である。
レーザはエネルギー密度が高く、方向性及び制御性が高いため、通常条件下での加工等で一連の優位性があるが、作用範囲が小さく表面処理にしか適さないという限界性がある。この限界をいかにして特徴として転化させ、強度と靱性の向上、形態と性質の改良、機能と性質の両立という側面を兼ね備えさせるか、さらには、より高い加工効率での金属加工品の力学特性の制御方法こそ、筆者及び研究グループが長年取り組んできた研究目標である。本稿では3つの典型的な実例を結び付けて、関連する研究成果及び実用化状況を紹介する。
2 レーザダル加工方法及びその実用化
2.1 技術的背景
プレス成型レベルの高品質なダル仕上げ金属薄板の製造には、ダル仕上げ用の圧延ロールを採用する必要がある。しかし、わが国の関連業界は知識不足により、海外の先進的な圧延設備を導入しても、中国製品は長きにわたり海外製品に比べて品質上大きな差が存在した。
中国における圧延ロールのレーザダル加工技術の開発及び実用化は1990年代初期に始まった。中国科学院力学研究所は1992年、首都鋼鉄公司鋼鉄研究所、中国大恒公司、北京吉普有限公司等の企業の協力の下、中国初のYAGレーザダル加工設備を製造して冷間圧延ロールのレーザダル加工技術を開発し、同年、中国初の精密帯鋼専門メーカー、秦皇島龍騰公司での応用に成功した。その後まもなく、武漢鋼鉄公司の協力の下、華中科技大学も中国初のCO2レーザダル加工設備の開発に成功した。1993年、国家科学技術委員会は圧延ロールのYAGレーザダル加工技術を国家重点科学技術普及事業として認定した。
2.2 圧延ロールのレーザダル加工の特徴
圧延ロールのレーザダル加工技術の原理とは、高い繰返し周波数及び高い出力密度のパルスレーザ(CO2レーザには機械で、YAGレーザにはQスイッチでパルスを調整)を用い、一定の分布(規則的またはランダム分布)に従い圧延ロール表層材料にマイクロスケールで溶融凝固加工をすると共に高圧気流を利用して設定した方向、位置、形態に溶体を移動し、堆積させるものである。このため、いわゆる圧延ロールのレーザダル加工とは実質上、レーザ及び気流を手段に圧延ロールの表面に一定のデザイン及び外観要求に基づいた顕微彫塑を行うプロセスである。
2.3 圧延ロールのレーザダル加工による寿命延長メカニズム
圧延ロールのレーザダル加工は平滑化プロセスのみならず冷間圧延プロセスにも応用できる。対比実験の結果(図1)が示すように、平滑化プロセスにおいては圧延対象は焼鈍した冷間圧延薄板であり、プレス率は一般に1%未満で、レーザダル加工圧延ロールの摩耗率はよく用いられるショット・ブラスト圧延ロールをはるかに下回り、圧延製品の長さも後者の2倍以上となる[図1( a)]。冷間圧延プロセスにおいては圧延対象は熱間圧延スラブであり、プレス率は50%を上回ることもあるため、汎用ロール(すなわち砥石ロール)に比べ、レーザダル加工圧延ロールの優位性は非常に顕著である[図1(b)]。
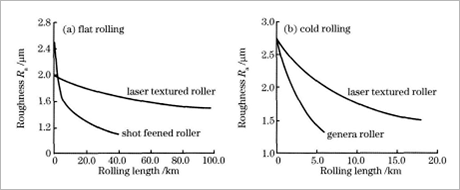
図1 さまざまなレーザダル加工方法による圧延ロールの寿命比較
2.3.1 表層の剰余圧縮応力強度の低減(圧力低減・靱性増加)
冷間圧延ロールの多くは、9Cr2Mo等の強度の高い合金鋼を用いて製造する。焼き入れは表層の硬度及び耐摩耗能力を向上させる重要な工程であるが、これにより生じる剰余圧縮応力は表層の脆性と割れリスクも増大させる。技術上、圧延ロールの靱性は往々にして焼き戻し温度を引き上げる方法により改善されるが、この方法では代価として表層の硬度が犠牲になる。
X線応力測定装置の測定結果(図2)に基づけば、レーザ加工したダル目の間隔または直径が等しい場合は、圧延ロール表層の剰余圧縮応力の強度はダル目に作用するレーザパルス数の増加に伴い低下するが、レーザパルス数が6を上回った時に初めて、剰余応力は引張応力の状態を示す。すなわち、一定のパラメータの範囲内では、レーザダル加工は圧延ロール表層の剰余圧縮応力の強度を顕著に引き下げ、靱性レベルを向上させることができる。
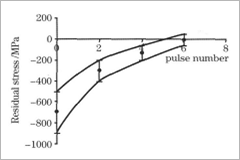
図2ロール面の剰余応力強度に対するレーザパルス数の影響
2.3.2 離散化による表層硬度の向上(性質改変・強度増加)
圧延ロールに対するレーザダル加工の際、レーザ出力密度は104 ~ 106 W/ cm2を超えることもある。パルスレーザのロール面に対する離散作用時間は約1sである。ダル目の溶融物の冷却および凝固は主に圧延ロール材料の良好な熱伝導率と圧延ロール自身の巨大な熱容量に依存する。このことから、冷却速度及びこれにより生じる凝固組織の洗練化及び硬度レベルは、通常の熱処理によるものに比べてはるかに高いだけでなく、連続レーザ加工によるものに比べてもはるかに高いことは想像に難くない。
2.3.3 接触条件の改善(形態改変・摩耗低減)
上述の通り、レーザダル加工により圧延ロール表面に形成されたマイクロ構造は、離散分布状の密閉微細凹部とこれに相対して平滑な凸包からなる。圧延ロールで圧延する際、これらマイクロ構造とロール鋼板との間には図3で示す接触状態が生じる。相互の咬み合わせが良好なため両者間に滑動は生じず、ロール鋼板表面に切り込みや溝は生じず、圧延ロールそのものも摩耗しにくい。また、密閉型の微細凹部であるために、凹部内の圧延により圧延ロールとロール鋼板が咬みあわせた後に高い圧力が生じることは、その潤滑作用の維持だけでなく、圧延ロールとロール鋼板とが張り付く可能性の低減にも有利である。張り付きは、薄板冷間圧延プロセスと焼鈍薄板の平滑化・圧延プロセスでよく見られる有害現象である。
レーザダル加工範囲の間隔と加工品の耐摩耗能力に関する実験によれば、レーザ強化範囲が相接する際に加工品の摩耗重量損失が最も小さく、すなわち、この時の加工品の耐摩耗能力が最も強い。
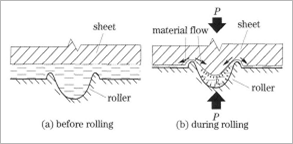
図3レーザダル加工によるロール面の外観改善及びそのロール鋼板との接触条件
2.4 レーザ加工によるダル薄板の性能最適化メカニズム
関連実験の結果によれば、平滑化したか否かを問わずプレス速度が1m/sを上回る時、レーザ板の摩擦係数は明らかにショット・ブラスト板を下回る。つまり、同一の成型条件下では、レーザ板の方が流動性が良く、成形能力が強い。光沢板、ショット・ブラスト板、放電板(電気スパークによりブラストした圧延ロール平滑鋼板)に比べ、レーザ板の映像明晰性が最も優れていた。そのうえ、レーザ蒸発型(微細凹部しかないダル加工圧延ロールの平滑化)鋼板の映像明晰性はレーザ溶融型(微細凹部だけでなく、凸包もあるダル加工圧延ロールの平滑化)鋼板を明らかに上回っていた。しかし、成形能力の面から考えると、材料の流動性は微細凹部の形態だけでなくサイズと関係する。このため、冷間圧延薄板製品の表面外観及び粗度は、主にその用途及び品質要求に基づき、統一的にデザインされる。
図4によれば、摩擦引張変形のない条件下で、08Fレーザによるダル薄板(厚さ0.35mm)の伸長速度は光沢板(すなわち、砥石ロール・フラインダーにより製造された鋼板)の約5倍であり、光沢板サンプル上では顕著な滑動移動及び圧縮は見られなかった。一方、レーザ板サンプルの滑動移動は多様性に富み、集中性におけるバランス喪失は滑動移動帯が相当に広い範囲で十分に進展した後に出現したものである。
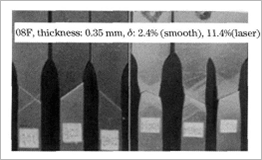
図4 08F鋼レーザ板と汎用板の引張性能の対比
走査型電子顕微鏡(SEM)による動態観察の結果によれば、レーザ板表面の事前変形・硬化部分(凸包和凹入部)は滑動線の運動に阻害効果をもたらし、すなわち、事前硬化部分にはレベリング、変形の安定化、変形集中の老化緩和作用があるため、レーザ板の塑性変形能力を向上させる機能がある。
薄板の引張変形損傷理論に基づけば、レーザダル薄板の表面粗度は安全閾値範囲内に制御される必要がある。冷間圧延された低炭素鋼薄板については、引張変形による表面損傷の極限スケールは、板厚の1%を上回ってはならない。
2.5 YAGレーザダル加工技術の進展・実用化概況
圧延ロール領域においては、板面接触条件の改善により帯鋼の焼鈍張付を防止する技術や表層の強度・靱性レベルの向上により圧延ロールの寿命を延長する技術がある。圧延機領域においては、圧延ロールと薄板間の摩擦条件の改善により圧延機の圧延速度を向上させる技術や、これらの作業による圧延ロールの粗度差を通じて汎用冷間圧延機上で非同期圧延を実現する技術がある。また、薄板製品については、輝度とプレス性能を兼ね備えた精密帯鋼及び鏡面鋼板の製造技術等がある。
現時点までに、中国が独自に開発した圧延ロールのレーザダル加工技術と設備はすでに冶金業界で広く認められている。レーザダル加工技術を応用した製品も当初の低炭素鋼板から、徐々に汎用鋼、合金鋼に拡大し、アルミニウム合金製品までも製造するようになった。レーザダル加工圧延ロールの応用は、冷間圧延の平滑化プロセスから冷間圧延プロセスにまで拡大し、ダル鋼板の製造を主な目標としていたものが圧延ロールの使用性能及び耐用年数の向上を主な目標とするまでになり、形態及び性質の改善、機能及び構造、強度及び靱性の向上という多くの目標を兼ね備える総合的な応用技術にまで拡大した。
3 レーザめっき層の強化方法及び実用化
3.1 技術的背景
高温強度、化学的安定性、耐摩耗能力に優れていることから、クロムめっき加工品は工業に広く用いられているが、加工品の寿命に影響する主な問題はめっき層にクラック・剥落が生じやすいことにある。これまでに開発されたさまざまな改良技術には、前処理(基体材質または基体そのものに対する強化処理等)、工程処理(電気めっきプロセスやめっき液の配合改善等)、後処理(めっき層に対する応力除去・焼鈍・再溶融等)があり、めっき層の早すぎるクラック・剥落の面で改善が見られるものの、総合的な効果の上では、進歩し続ける工業技術の要求を満たしていない。
われわれが報告する技術プランは、クロムめっき工程前に、まず基体にレーザ熱離散処理をするものである。ある種の鋼を基体としたクロムめっき部品は、高温、高圧、強い融蝕環境を何度も経なければならない。そのため、この技術的難題に対しては何度も試みがなされており、既存のさまざまな技術が応用されてきたが依然として寿命は基準を満たさず、次に述べる技術プランが採用されるまでは実用上の課題となってきた。
3.2 技術的特徴及び応用効果
基体のレーザ前処理により形成されるクロムめっき層の構造を図5に示す。
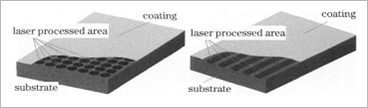
図5 基体に対するさまざまな離散方式によるレーザ前処理クロムめっき複合材料の構造
ある種の鋼を基体としたクロムめっき部品に設計された総合寿命はのべ3000回転であったとしても、既存の処理方法では総合寿命はのべ2000回転にしかならない。基体に対するレーザ前処理方法を採用した後にその総合寿命はのべ3000回転を超え、さらにレーザ工程を改善したところ総合寿命は一層高まり、のべ4500回転に達した。
図6(a)、(b)はそれぞれレーザ前処理後、及びレーザ処理を行っていないクロムめっき部品であり、(a1)、(a2)、(a3)ならびに(b1)、(b2)、(b3)はそれぞれ出口、中ほど、燃焼室に近い部位のめっき層の寿命状態を示している。この図ではレーザ前処理方法の効果がはっきりと示されており、(a)部品のめっき層の剥落及び摩損程度はどの部位においても(b)部品を下回っている。
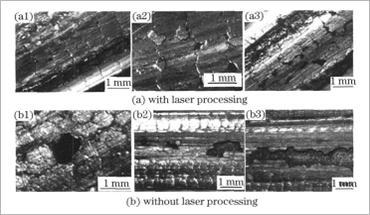
図6 レーザ離散による前処理部品及び未レーザ処理部品のめっき層の失効状況の対比(表面)
断面図(図7)を見ると両者の差が更にはっきりと見て取れる。熱・機械衝撃(熱、化学及び機械力の相乗作用)のべ3000回転以降、(a)部品の孔部めっき層はなおも基本的に完全を保ち、燃焼室近くの部位も著しく融蝕したもののめっき層の残留を維持した。一方、(b)部品は熱・機械衝撃のべ2000回転で、対応部位のめっき層はほとんど消失し、燃焼室近くの部位の基体におけるクラック現象は深刻であった。
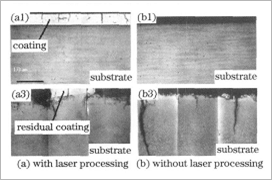
図7 レーザ・未レーザ処理部品の寿命時におけるめっき層失効状況の対比
2種類のめっき層に対する超音波腐食試験の結果によれば、レーザ前処理めっき層の耐腐食能力は既存技術のめっき層を明らかに上回った。
3.3 レーザによる寿命延長メカニズムの分析
3.3.1 性質改変・強化メカニズム
レーザ前処理後、基体表層材料は性質改変により硬化され、クロムめっき層と基体の原始組織との間の硬度の激しい格差もこれにより緩和される(図8参照)。加工品表層の寿命については初期硬度曲線[図8(b)]が示すように、のべ3000回の熱・機械循環後、加工品は全体的に軟化し、めっき層の硬度現象も特に著しいが、めっき層とレーザ強化部位の硬度は依然として基体の原始組織を上回る。このことは、加工品の寿命全うにおけるレーザ前処理の意義を充分に体現するものである。
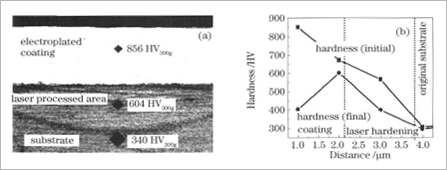
図8 クロムめっき層体系の硬度に対するレーザ前処理の影響
3.3.2 構造性能の遺伝メカニズム
SEMに対する観察に基づけば、レーザで前処理したクロムめっき層の界面構造[図9(b)和(d)]の精巧さ、緻密さ、クリーン度は一般の電気めっき層より明らかに優れている[図9(a)及び(c)]。透過型電子顕微鏡(TEM)による組織及び回折分析によれば、レーザで前処理しためっき層組織のサイズは一般のめっき層より明らかに小さい。ナノ硬度実験によれば、レーザで前処理しためっき層の力学特性も一般のめっき層をはるかに上回る。めっき層の成長プロセスにはレーザによる作用はないことを鑑みれば、2種類のめっき層の組織及び性能の差はそれらの基底によるとしか考えられないため、基底はめっき層に対して強い遺伝効果があると言える。
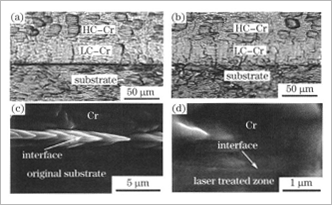
図9 めっき層界面構造に対するレーザ離散熱加工の影響
3.3.3 強度・靱性の相乗メカニズム
レーザによりめっき層を前処理した部品が使用される際、硬質部分が外的負荷を支え、抵抗する主力となり、靱性部分は硬質部分が外的負荷を支え、抵抗するプロセスで生じる応力と変形を緩和し、吸収しうる。このため、これらの強度・靱性構造はめっき層におけるクラックの形成を効果的に減らし、かつ、遅らせることができる。
クロムのめっきプロセスにおいては、クロム原子の沈積、結晶核生成及び成長によりめっき層内の応力が徐々に増大し、クロムめっきの断裂強度を超えるまでになる。このため、未使用のクロムめっき層であったとしても、その内部には往往にして大量の微小なクラックが存在する。使用プロセスにおいては、初期の内的応力と外的負荷の相乗作用の下で、めっき層中の一部の局部部位における微小なクラックが繋がって成長し、めっき層の厚さ全体を表面から内部まで貫通し、基体にまで達する分割性を持つクラックにまで徐々に発達する。この種のクラックは製造工程では歓迎されるものではないが、往々にして回避できない。
レーザ離散により前処理された基体は、剰余応力分布を制御することでめっき層の分割性クラックの間隔を調製することができる。使用の際、これら分割性クラックはレーザスキャナの道筋と平行で、レーザ前処理離散度と平行に走るすじ状の主要クラックに成長しうる。
めっき層の基体に対する防護の面から見ると、めっき層中の主要クラック数の減少が望まれる。それは、熱環境による基体への損害を低減するのに効果的であるためである。しかし、主要クラックにより界面応力(界面破壊駆動力とも言う)を低減するという観点から見れば、主要クラックの間隔について、それが効果的に作用を発揮できる範囲内に制御することを望むなら、図10に示す応力曲線の左側に制御する必要がある。
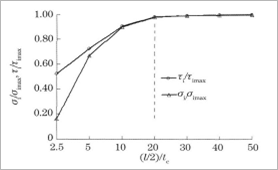
図10 界面の参考ノード応力とクラック間隔との関係
3.4 めっき層の界面結合性能の特徴
レーザ強化めっき層により派生する新たな問題とは、強結合めっき層の界面性能をいかに表現し、評価するかである。界面結合強度が90MPaを下回るめっき層については、製造工程では接着引張や湾曲等の既存の方法によりその界面性能を評価している。鋼基クロムめっきは強結合めっき層体系に属し、レーザ前処理を経た後にその界面強度がさらに高くなるため、相応する海綿性能の表現方法が急ぎ必要とされている。
このため、図11に示す側面圧入方法が進められた。この方法では円錐形の圧子をめっき層サンプルの基体の片側に圧入し[図11(a)]、基体材料からの膨出によりめっき層のクラック[図11(b)]及び剥落[図11(c)]が生じる。
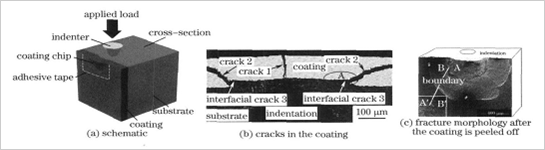
図11 側面圧入方法
4 レーザ補助プレストレス力による成形方法
4.1 技術的背景
成形は機械製造領域における重要な製造方法の一つである。ここで言う成形製造とは、特に板金部品、すなわち薄壁またはコアシェル類部品を湾曲または引張曲げ等の方法により変形することで、設定したサイズや形状を実現する加工プロセスである。この種の成形・製造プロセスには、その構造が・形状が複雑なために(例えば、馬の鞍型の加工品)、あるいは網状に張られた強い鉄筋による支柱作用のために(例えば、全体壁板等)、上記の方法で成形目標を実現するのが難しい種類の板金部品がある。
現時点で、これら部品の成形上の難題を解決する主な方法はショット・ブラスト及び時効法である。ショット・ブラスト法は自由ショット・ブラスト成形及びプレストレス力ショット・ブラスト成形の2種類に分けられる。時効成形はまたの名をプレストレス力高温クリープ成形という。この方法は、金型上でクランプされ、かつ、弾性湾曲負荷を与えられた部品の全体を加熱罐に入れ、高温条件下(アルミニウム合金部品に対しては一般に110℃~170℃で20h保温)でクリープ作用により成形を実現するものである。
時効成形の能力はショット・ブラストを上回るが、時効成形部品は時効強化材料を採用して制作して初めて、熱軟化効果を克服できる。ショット・ブラスト成形の際は、部品表層の変形抵抗力が増大し続けるため、成形能力は総体的に小さく(金型を使用しないショット・ブラストの成形能力はさらに低い)、大スケールまたは高い骨格に支えられた薄壁部品は必ず中間焼鈍を経る必要がある。レーザ補助プレストレス力による成形方法は上記の限界性の克服に役立つ。
4.2 レーザ補助プレストレス力による成形方法の原理
レーザによる溶接、切断、クラッディング、表面熱処理方法、レーザによる急速原型製造とレーザ湾曲による成形方法は異なる。後者の方法による成形の主なエネルギー源は部品の弾性内部エネルギーであり、レーザの主な作用は部品の弾性内部エネルギーが集中する部位の材料の変形抵抗力を低減し、弾性エネルギーにより塑性を作り、部品の湾曲成形を実現することにある。
構造の複雑な、あるいは骨格に支えられた薄壁部品の弾性内部エネルギーは、往々にしてその幾何学的な急変または骨格のある部位に集中するため、レーザ補助プレストレス力による成形の際は、レーザはこれら部位についてだけ干渉すれば足りる。壁板全体の部品の弾性内部エネルギー分布数値の計算結果(図12)によれば、90%の弾性内部エネルギーは表面積が10%を超えない構造強化部位(図中の発光部位)に集中する。このため、これら部品に対しては、いわゆるレーザ補助成形はこの10%の部位について実施すれば足りる。

図12 壁板全体の湾曲の際の弾性内部エネルギーの分布
4.3 成形效果の例
4.3.1 薄板サンプル
アルミニウム合金、低炭素鋼、チタン合金等のよく用いられる成形材料薄板サンプルに対してレーザ補助成形実験を実施した。結果は図13に示すように、異なる材質サンプルに対するレーザ補助成形による能力の上昇幅は異なるが、その効果はいずれも顕著であった。
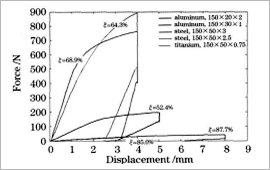
図13 薄板に対するレーザ補助成形の負荷移動曲線
4.3.2 壁板全体(肋条支撑)サンプル
7075アルミニウム合金の壁板全体サンプルにレーザ補助成形及び時効成形をそれぞれ実施した結果を図14に示す。レーザ補助成形の作用時間は30minで、負荷除去後のサンプル成形の高さは12.5mmであった。時効成形の技術パラメータは170℃、22.5hで、負荷除去後の成形の高さは13.6 mmであった。

図14 7075アルミニウム合金構造サンプルのさまざまな方法による成形效果
実験により、初期の弾性内部エネルギー(すなわちサンプルのたわみ)が一定の状況下では、サンプルの弾性内部エネルギーの転換効率はレーザスキャンの回数の増加に伴い低下し、スキャンを7回繰り返した後のエネルギー転換は飽和に向かうため、サンプルの成形量を継続的に引き上げたい場合は適時にそのたわみを引き上げる必要があることが分かった。
4.3.3 サンプルの性能に対するレーザ補助成形の影響
被覆アルミニウムとアルミニウム合金2024に対する対比実験に基づけば、レーザ補助成形の前後は、2種類のサンプルの組織構造の間には明確な差は見られなかった。レーザ補助成形サンプルの疲労寿命は、レーザ作用部位の材料に熱軟化が生じたために低下したものと考えられる。しかし、これら部位にショット・ブラスト強化処理を行いさえすれば、レーザ補助成形サンプルの疲労寿命は低下しないばかりか、初期材料を上回る可能性さえある。
5 結論
上述した新技術及びそれらの応用效果は次の通り。
- 圧延ロール表面のレーザ離散による溶融凝固処理により、デザインされた外観及び粗度での製造が可能であり、表層の靱性を向上させるとともに高性能の溶融凝固組織を得ることができ、圧延ロールの使用效果及び耐用年数をめざましく改善することができる。
- 基底表面に対するレーザ離散前処理により、基底の強度を向上させられるばかりでなく、基底とめっき層の界面結合能力をめざましく向上させることができ、めっき層の組織及び性能を改善することもできる。
- レーザ局部熱による軟化補助プレストレス力により、損傷を与えず性能を向上させられる前提下で、金属加工品、特に複雑な金属構造を持つ加工品の成形能力を向上させることができる。